Lubrication management lies at the foundation of machine reliability. Without good lubrication practices in place, you run the risk of breakdowns, costly repairs, lubricant waste, and other mishaps. With that said, developing and managing an effective lubrication program requires significant attention to detail and willingness to dedicate time and resources. This article outlines key considerations for building your lubrication program and best practices for effective lubrication management.
The Six Lubricant Lifecycle Stages
The first step in optimizing your lubrication program is understanding the entire lubricant lifecycle. Noria’s ASCEND™ methodology offers a structured approach to lubrication management, dividing the lifecycle into six distinct stages from reception to disposal. Each stage involves a set of best practices that contribute to overall lubrication excellence and machine reliability.
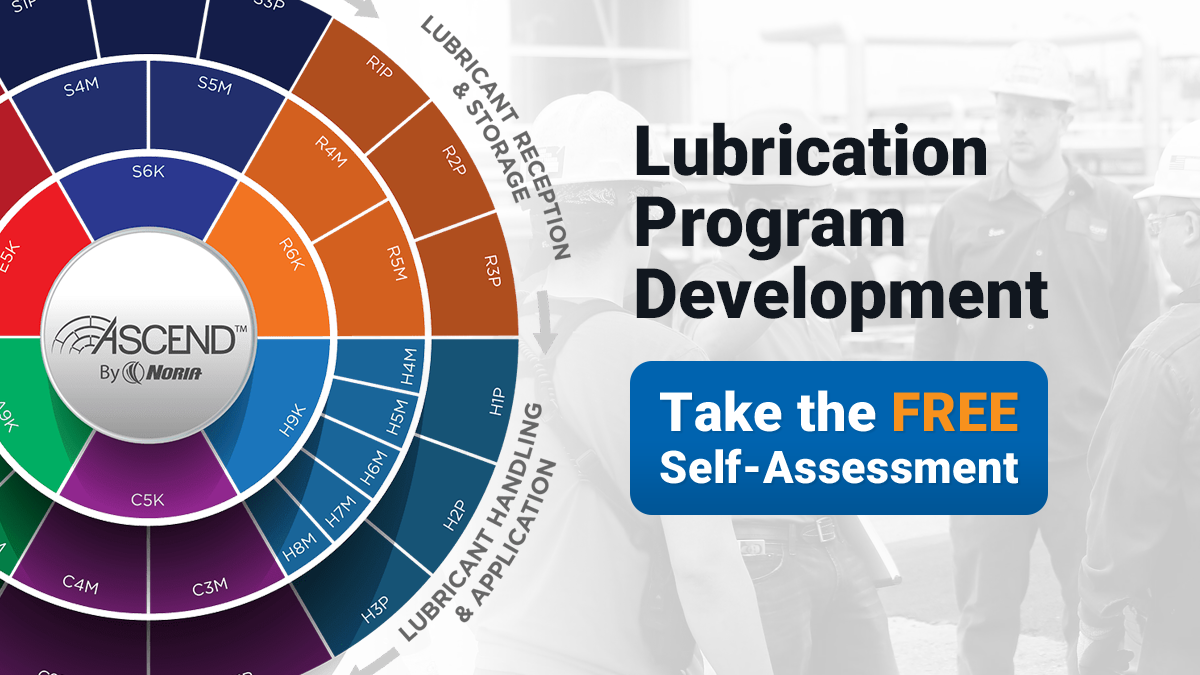
1. Selection
Choosing the right lubricant is the first and one of the most crucial steps in the lubricant’s lifecycle. The selected lubricant must meet the specific performance requirements of the machinery and its operational environment. This involves understanding the machine’s operating conditions, such as temperature, load, speed, and environment, and matching these with the lubricant’s properties.
Key Considerations:
- Compatibility with equipment materials and seals
- Resistance to temperature extremes and oxidation
- Ability to minimize friction and wear
- Environmental impact and compliance with regulations
2. Reception & Storage
Once selected, the lubricant must be received in the correct condition. This stage involves testing to confirm the lubricant is not contaminated during transportation and arrives in its intended state. From there, it must be stored in an environment that keeps it clean, cool, and dry.
Key Considerations:
- Use of sealed containers and proper labeling
- Storage in cool, dry, and clean areas away from direct sunlight
- Regular inspection of storage conditions and lubricant containers
- Use of appropriate transfer equipment to minimize contamination risks
3. Handling & Application
Applying the lubricant correctly is critical to maximizing its effectiveness. This stage includes applying the lubricant in the correct location, using the right tools, and transferring it from storage to the equipment with clean containers. Precision in application—right amount, right frequency—is key to avoiding under-lubrication or over-lubrication, both of which can cause significant issues.
Key Considerations:
- Training personnel on correct application methods and tools
- Machinery configuration based on optimal reference state
- Lubrication routes designed for optimization of workloads, resources, and personnel
- Use of automated lubrication systems where appropriate
4. Contamination Control & Reconditioning
Contamination control is essential for maintaining the integrity of the lubricant throughout its lifecycle. This stage involves protecting the lubricant from contaminants such as dirt, moisture, and other foreign materials during storage, handling, and application. Implementing filtration systems, using proper storage containers, and following best practices for handling can significantly reduce the risk of contamination.
Key Considerations:
- Use of desiccant breathers to remove particles and moisture from oil
- Use of clean storage and transfer equipment to prevent exposure to contaminants.
- Use of filtration, centrifugation, and dehydration to remove contaminants and restore lubricant properties.
- Maintaining clean, controlled environments in storage and handling areas.
5. Monitoring, Analysis, & Troubleshooting
Lubricant analysis is a powerful tool for monitoring the condition of both the lubricant and the machinery. Regular analysis helps detect contamination, degradation, or any other issues that could impact machine performance. By tracking the condition of the lubricant over time, reliability professionals can make informed decisions about when to change or recondition the lubricant.
Key Considerations:
- UEstablishing a routine lubricant analysis schedule.
- Monitoring key indicators such as viscosity, contamination levels, and additive depletion.
- Using analysis results to adjust lubrication schedules or select alternative lubricants.
6. Energy Conservation, Health & The Environment
The final stage of the lubrication lifecycle is disposal, which is critical for environmental compliance and safety. This stage involves safely removing and disposing of old lubricants according to regulatory standards, as well as considering options for recycling or reconditioning where possible.
Key Considerations:
- Environmental regulations over the disposal of lubricants
- Correctly managing lubricant leaks and spills
- Reducing energy consumption by minimizing friction with correct lubricant selection and application
Best Practices for Lubrication Management
Now that you’re aware of considerations for each stage in the lubricant lifecycle, it’s time to cover tips for effective lubrication management. To truly excel in this area, organizations must not only implement sound lubrication practices but also invest in the right tools and training. The value of comprehensive lubrication training cannot be overstated—it equips maintenance teams with the skills needed to apply lubricants accurately and manage them effectively. Additionally, leveraging lubrication management software helps streamline processes, automate scheduling, and provide data-driven insights for continuous improvement. Equally important is designating a program leader to oversee and drive the lubrication strategy and enforce best practices across the organization. Together, these elements form a robust framework for optimizing lubrication management and enhancing overall operational performance.
Have a Dedicated Program Leader
Appointing a dedicated lubrication program leader is essential for ensuring best practices are consistently applied and maintained across the organization. This leader acts as a central point of accountability, overseeing the development, implementation, and continuous improvement of the lubrication program. A program leader also plays a crucial role in fostering a culture of proactive maintenance, coordinating training efforts, and integrating new technologies like lubrication management software.
Invest in Lubrication Training
Investing in lubrication training is crucial for a successful lubrication program. While lubrication might seem like a straightforward task, the nuances of selecting, applying, and managing lubricants require a deep understanding and specific skill set. Proper training equips those involved in lubrication activities with the knowledge and expertise needed to execute these tasks with the necessary precision.
For those getting started with lubrication or have not had any previous formal training, it is recommended to start with Machinery Lubrication I, which covers foundational knowledge including lubricant selection, contamination control, storage and handling considerations, inspections, and more. From there, advanced courses such as Oil Analysis II, Machinery Lubrication II, and Machinery Lubrication Engineer can help to expand lubrication knowledge and further improve the program.
Implement Lubrication Management Software
Due to the abundance of procedures, inspections, and data associated with lubrication, it is recommended to use dedicated software to keep everything organized. Lubrication management software (LMS) helps to streamline lubrication processes, track program success, and execute all tasks efficiently.
Why not manage lubrication tasks in a CMMS alongside other maintenance tasks? A few reasons. First, there are typically several lubrication tasks that need to be completed daily (and sometimes even multiple times a day). A CMMS specializes in PMs that are done routinely but typically not at this frequency. This results in too many tasks, leading to missed work from the CMMS. Another reason is the critical information needed to accurately lubricate a piece of equipment is seldom codified and associated with the CMMS asset list or hierarchy. This information might include detailed inspection points, the volume of lubricant, the type of lubricant, the proper procedure to lubricate the component and other pertinent data.
Let’s take a look at the key features of LubePM, the leading lubrication management software:
Centralized Data Management
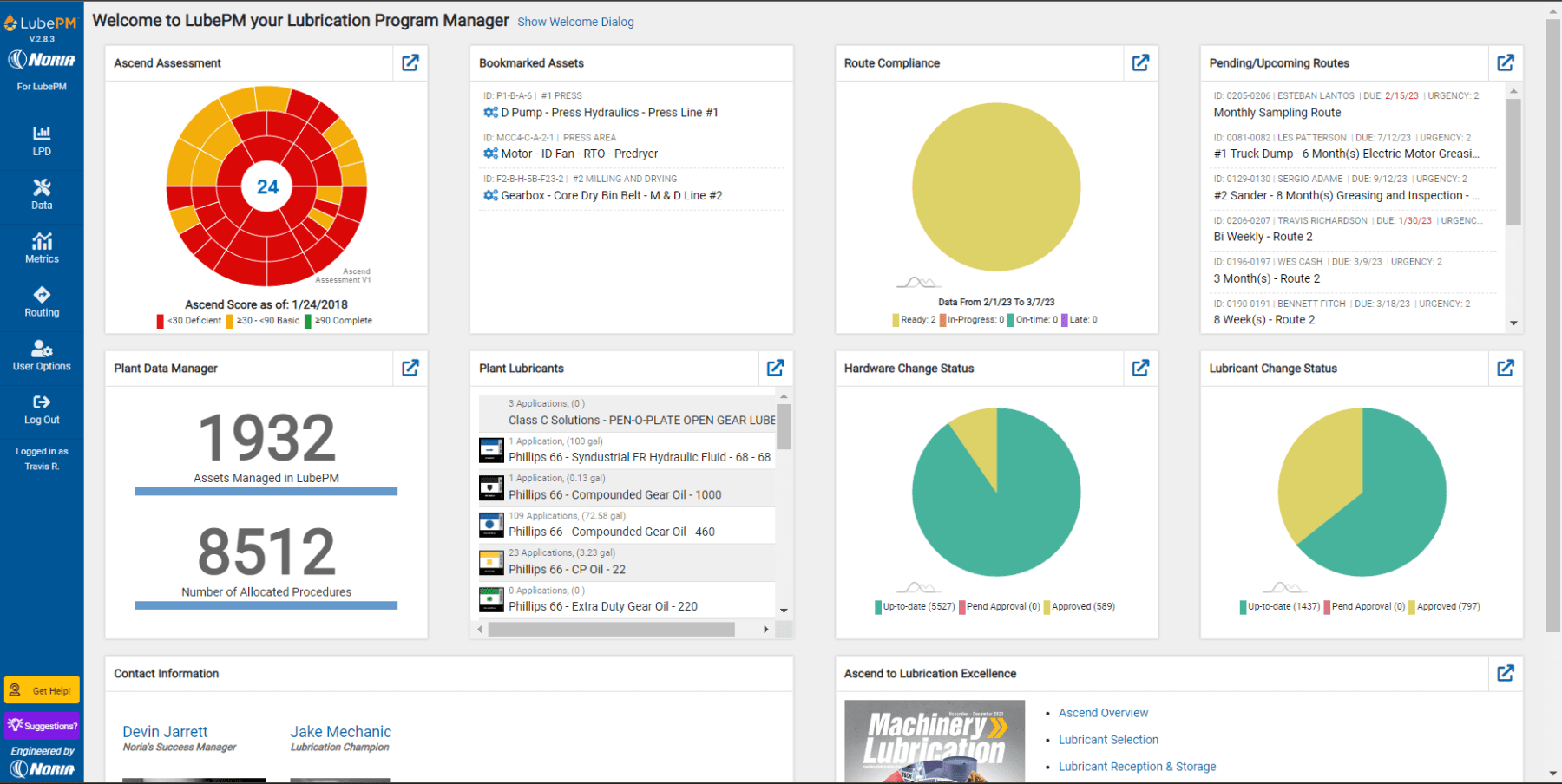
Lubrication management software centralizes all lubrication-related data, including lubricant specifications, application schedules, and inspection data. This allows for easy access and sharing of information across team members.
With all data in one place, it becomes easier to track the lifecycle of each lubricant, from selection to disposal, and to make sure the program is consistently improving. Systems like this also come in handy when there is turnover in an organization. Instead of all program knowledge going out the window when someone resigns or retires, it stays put within the LMS.
Automated Route Scheduling and Alerts
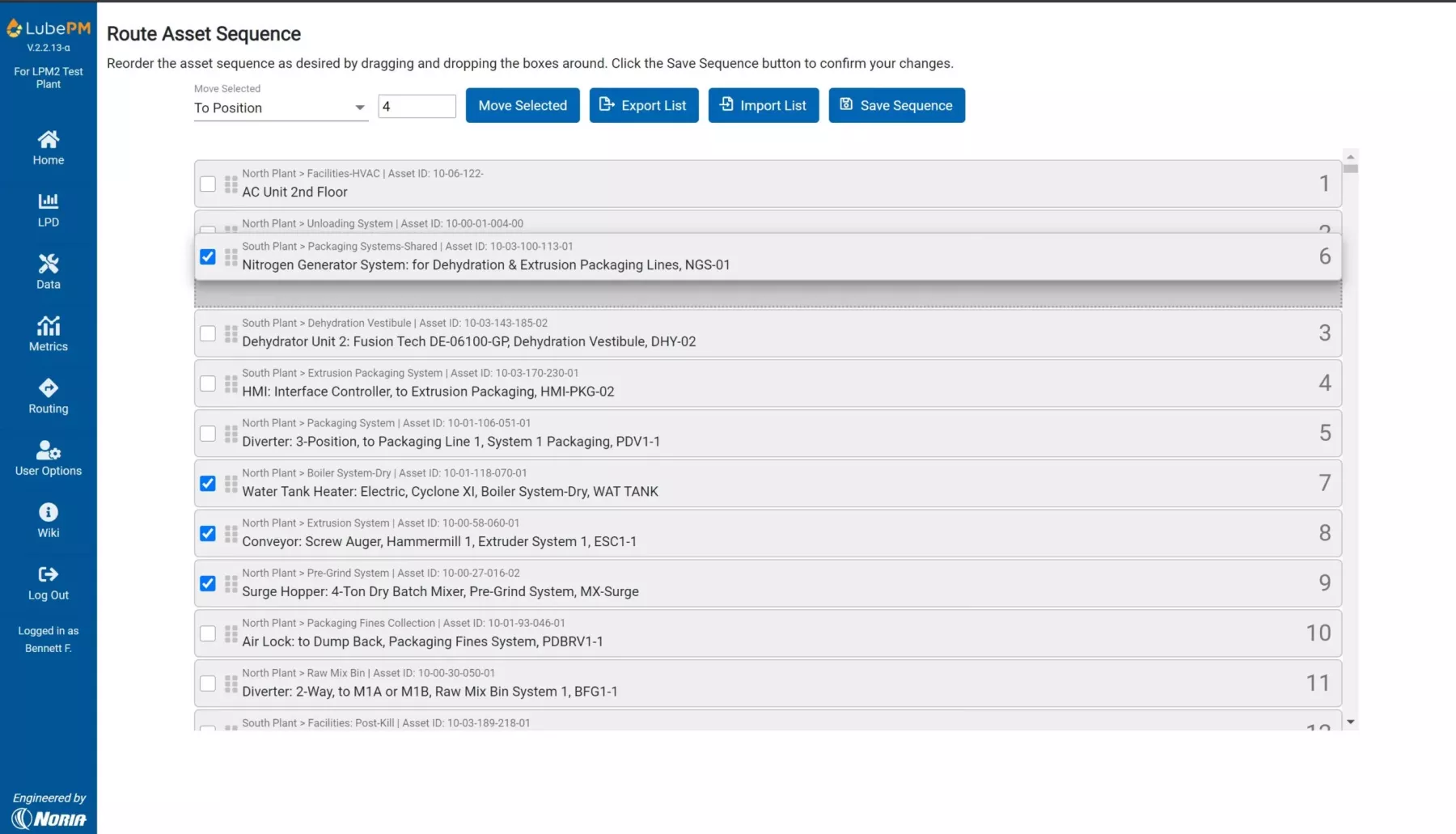
One of the key advantages of using LubePM is the ability to automate lubrication schedules. Maintenance teams can easily generate detailed lubrication routes that outline specific tasks, frequencies, and locations for each piece of equipment. The software allows for the customization of these routes based on the unique needs of the machine in terms of the right type and amount of lubricant at the right time.
Additionally, the software can send alerts and notifications for upcoming lubrication tasks, overdue activities, or when a lubricant needs to be analyzed or replaced. This proactive approach helps in maintaining optimal equipment performance and preventing issues before they arise.
Detailed Reporting and Analytics
Lubrication management software provides powerful reporting and analytics tools that enable users to analyze the success of the lubrication program over time. These tools help identify trends, detect potential problems, and optimize lubrication intervals based on real data. Reports generated by the software can include information on lubricant use, hardware recommendations, cost savings, and more. This data-driven approach allows for continuous improvement in lubrication practices and supports informed decision-making.
Bottom Line
Effective lubrication management is a vital component of a successful maintenance strategy, directly impacting equipment reliability. By investing in comprehensive lubrication training, employing advanced lubrication management software, and appointing a dedicated program leader, organizations can create a structured and proactive approach to lubrication. These best practices not only help in preventing costly equipment failures but also optimize the use of resources, reduce downtime, and extend the life of critical assets.
Want to take the guesswork out of lubrication management? Learn more about LubePM lubrication management software.