Kronospan is one of the largest manufacturers of wood-based panels in the United States. With operations across multiple facilities, the company is dedicated to innovation, quality, and sustainability in its products. However, as their operations expanded, maintaining machine reliability and minimizing downtime became increasingly challenging.
In 2021, Kronospan (formerly Woodgrain) set out to overhaul their lubrication program to reduce downtime and improve machine reliability. Historically, their maintenance program relied heavily on tribal knowledge without written procedures, creating significant challenges. Recognizing the need for change, Kronospan prioritized developing a purposeful maintenance and reliability culture. Their goal was to foster trust and communication between management and their three-person lubrication team while streamlining their overall maintenance processes.
Driving Success with LubePM
At the heart of this transformation was Kronospan’s adoption of LubePM, a Lubrication Management System. This cloud-based software became a cornerstone of their program, helping the team track lubrication tasks, manage inventories, and ensure compliance with new written procedures. Robust data tracking allowed them to identify potential issues before they caused unplanned downtime, while scheduling tools ensured lubrication tasks were completed efficiently and consistently.
The use of LubePM also helped Kronospan’s team establish measurable key performance indicators (KPIs), enabling them to quantify their progress and focus on continuous improvement. Since implementing the platform, along with other lubrication initiatives, they have saved approximately $655,000 by avoiding downtime caused by contamination and bearing-related failures.
Building a Reliable Foundation
Kronospan’s journey began with an ASCEND™ assessment conducted by Noria—a 524 point on-site assessment designed to identify gaps in their lubrication practices. The results revealed that downtime was costing the plant $9,000 per hour, making a well-designed lubrication program critical for operational success. With tribal knowledge diminishing as experienced staff retired, the team understood the urgency of implementing a sustainable, data-driven solution.
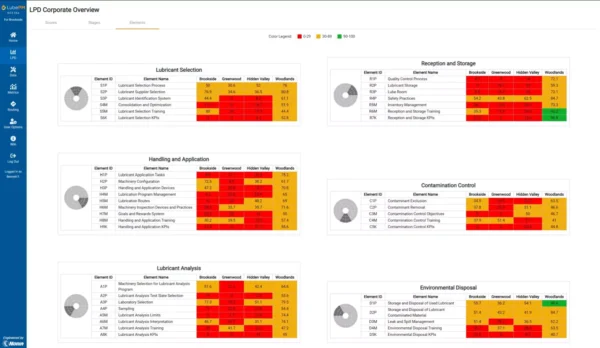
The assessment results provided a roadmap for success, highlighting parts of the program that need the most attention (shown in red). As time went on and improvements were made, the red areas slowly turned to green, indicating the implementation of best practices. In 2021, Kronospan reported 3,500 downtime minutes in their bearing equipment class. By 2023, that number had dropped to just 495 minutes—a dramatic improvement achieved through the team’s enhanced lubrication practices.
Modernizing the Lube Room
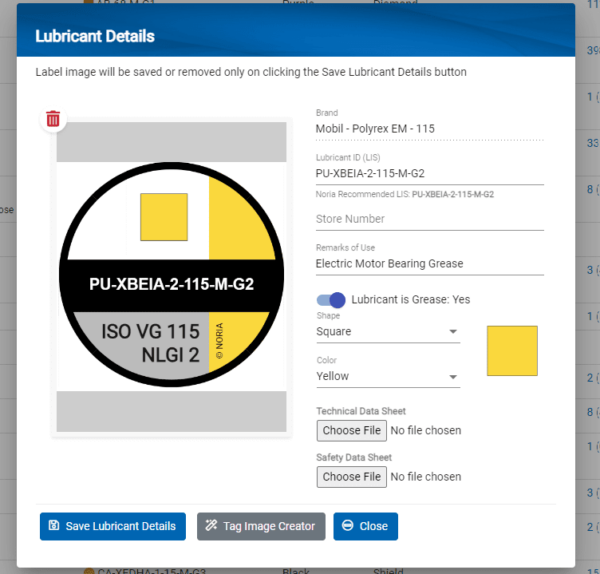
A key element of Kronospan’s transformation was the construction of a state-of-the-art lube room. Designed with efficiency and safety in mind, the room features OilSafe fireproof cabinets, 55-gallon drum workstations, and an oil analysis station. The centralized setup, paired with the task management and labeling capabilities of LubePM, has played a significant role in the success and organization of the lube room.
Streamlining Lubricant Selection
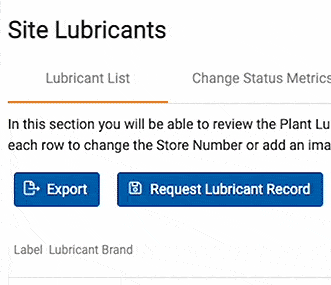
Kronospan leveraged LubePM’s database to optimize their lubricant selection, reducing the number of on-site lubricants without compromising machine reliability. LubePM offers a database to list all lubricants on-site, providing an “always current” plantwide lubricant list. This feature enables the team to manage changes for consolidation and best practices with integrated approval processes. Supported by detailed written procedures organized by equipment type, this process has become the new standard for the team. LubePM’s labeling and tracking capabilities ensure that all lubricants are properly stored and filtered, further enhancing equipment reliability.
Investing in Oil Analysis and Condition Monitoring
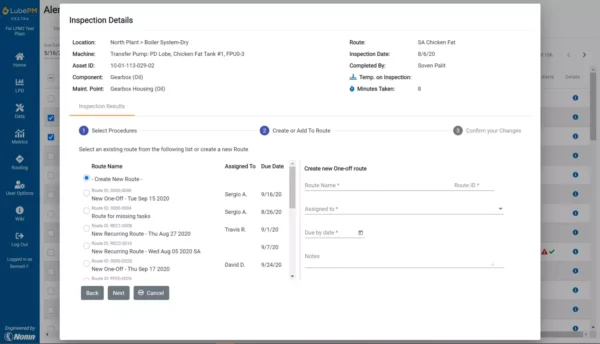
Kronospan’s team also expanded their use of oil analysis, using LubePM to document sampling procedures and create recurring tasks to ensure samples are taken at the correct intervals. Additionally, the team uses LubePM to upload sample and visual inspection data, enabling them to make informed decisions and further reduce failures related to lubricant condition.
Looking Ahead
Kronospan’s experience with LubePM highlights how a comprehensive lubrication management system can transform operations. By documenting sampling procedures, streamlining tasks, and utilizing advanced tools, they’ve built a reliable foundation for success. With significant improvements already achieved—such as a dramatic reduction in downtime and enhanced safety—the team is committed to continuing their journey of improvement. As they expand initiatives like ultrasonic greasing and vibration analysis, Kronospan exemplifies how innovation and a focus on reliability can drive lasting results in industrial maintenance.
Ready to take your maintenance program to the next level with LubePM? Reach out to a LubePM rep today.